Key Publications and Presentations:
MTR is the leading supplier of membrane system for hydrocarbon recovery from petrochemical plant vents.
Opportunity
During the production of polypropylene (PP), a portion of the propylene feedstock is lost. The value of the lost feedstock is substantial, ranging from $1 million to $3 million per year for a typical polypropylene plant. Propylene losses occur primarily in resin degassing vents.
VaporSep® Solution
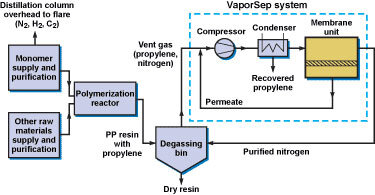
This propylene/nitrogen recovery unit was recently started up in Asia
For resin degassing applications, the vent stream is compressed and then cooled to condense the propylene. The gas leaving the condenser still contains a significant amount of propylene. This gas is fed to the membrane unit, which separates the stream into a propylene-enriched permeate stream and a purified nitrogen residue stream. The permeate is recycled to the inlet of the compressor and then to the condenser, where the propylene is recovered. The purified nitrogen stream is recycled to the degassing bin.
For C3 splitter overhead applications, the VaporSep unit is very simple, consisting of membrane modules only, with no moving parts. The stream leaving the column overhead is primarily propylene, mixed with light gases such as N2 or H2. The VaporSep unit splits this stream into a propylene-enriched stream and a light-gas-enriched stream. The propylene-enriched stream is returned to the distillation column, where the propylene is recovered, and the light-gas-enriched stream is vented or flared.
VaporSep units are currently used by major polypropylene producers including Formosa Plastics, Ineos, SABIC, Sasol, and Sinopec.
Benefits
- Recovers valuable propylene with typical payback time of less than 1 year
- Purifies nitrogen for reuse in the process
- Minimizes installation time and expense with skid-mounted construction
- Reduces incineration and flare requirements
- Achieves significantly higher hydrocarbon recovery than possible by condensation alone
- Allows recovery at more moderate temperatures and pressures than condensation alone
- Minimizes footprint and weight
- Creates no secondary waste streams

This propylene/nitrogen recovery unit was recently started up in Asia
System Performance
- Suitable for vent streams from 300 to 10,000 lb/h, with propylene concentrations from 10 to 80 vol%
- Propylene recovery up to 99+%
- Nitrogen recovery over 95% with purities of 99+ vol%
System Description
- Complete skid-mounted unit includes membrane modules, compressor, heat exchangers, piping, instrumentation, and controls
- Unit dimensions: 15 ft (L) x 10 ft (W) x 10 ft (H); 5,000 to 15,000 lb; compressor is mounted on a separate skid of similar size
- Conforms to typical petrochemical specifications (ASME, ANSI, PED, TEMA, NEC or IEC etc.)
- Control is by local PLC or through DCS